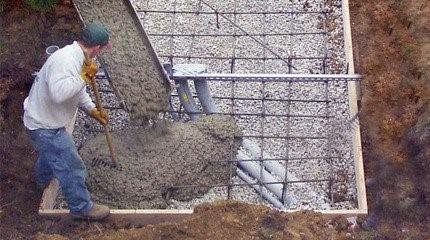
What is Building Foundation- The Complete Guide (2021)
What is a Building Foundation
A foundation is the very base of any building structure. The foundation transfers the load from the structure to the soil and also provides resistance from loads exerted by the earth. Making the foundation is a crucial process. Let’s have a look into the details of a building foundation. By the time you finish reading this article, you would have a good insight into the various aspects related to the Building Foundation of building structure.
TYPES OF FOUNDATIONS
- Shallow foundations
- Deep foundations
The words shallow and deep simply denote the depth of the soil excavation made for the formation of the Building Foundation.
Shallow Foundations
Shallow foundations are generally made 3ft to 5ft(1m-1.5m) deep.
Shallow foundations are also referred to as “Open footings” or “Spread footings”. The reason being, in the early work stages, the whole footing is completely visible to the eyes. For making the foundations, the soil is excavated till the bottom of the footing first, and then, the footings are constructed.
The idea behind this is that every footing bears the concentrated load from the columns and then spreads it out over an outsized area. It ensures that the particular weight of the soil does not exceed the safe bearing capacity of the soil.
Types of shallow footings:
- Individual Footings
- Combined Footings
- Strip Footings
- Raft Foundations
Individual Footings
Individual footings are one among the foremost simple and customary sorts of foundations. These are used in case the load of the building is borne by columns. Generally, each column has its own footing. The footing is simply a square or rectangular pad of concrete on which the column sits.
To get an estimation of the dimensions of the footing, an engineer would take the entire load on the column and divide it by the Safe Bearing Capacity (SBC) of the soil. For example, in the case of a column with a vertical load of 10 Ton, and the soil SBC=10 Ton/m2, the area of the footing will be 1 m2. In practice, the designer checks for several other factors before preparing a construction design for the footing.
Combined Footing
A combined footing is made when two or more columns are close enough and their isolated footings overlap one another. It is a mixture of isolated footings, but their structural design differs.
The shape of this footing may be a rectangle and is employed when loads from the structure are carried by the columns.
Strip Footings
Strip footings are commonly seen in load-bearing masonry constructions They act as an extended strip that supports the load of the whole wall. These are used when the building loads are carried entirely by walls instead of isolated columns, like in older buildings made from masonry.
Raft foundations
Raft foundations also called mat foundations sometimes, are used most frequently when basements are to be constructed. In raft foundations, the whole basement floor slab becomes the Building Foundation; the load of the building is spread evenly over the whole footprint of the building. It is called a raft because the building is sort of a vessel that “floating”’ in the sea of soil.
Mat foundations are used where the soil is weak or loose, and thus building loads must spread over a bigger area, or where columns are closely spaced. Hence, if individual footings are to be used, they would touch one another.
Deep Foundations
Deep foundations are generally made at depths of 10- 200ft (3m – 65m).
A pile, which is essentially an extended cylinder of robust and strong material like concrete, is pushed into the earth so that a building structure can be supported on top of it.
Following cases see the use of Pile Foundations:-
- When there’s a layer of weak soil at the surface that cannot support the weight of the building. Loads from the building must bypass this weak layer and be transferred to the stronger soil or rock layer underneath.
- When a building has very heavy, concentrated loads, like a high-rise structure.
Selection Criteria For Foundation
Selection criteria for a foundation for buildings depend upon two factors, i.e. factors associated with ground (soil) conditions and factors associated with loads from the structure. The performance of the Building Foundation is predicated on the interface between the loadings from the structure and therefore the supporting ground or strata.
The nature and conditions of each of those vary. Therefore, the choice of the appropriate foundation becomes necessary for these variations counting on circumstances.
Foundation Selection Criteria for Buildings
Loads of Structure
Loading conditions coming from and associated with the structure are one of the many factors that govern foundation selection. It is influenced by the type of building and construction material, environmental factors, and earthquake susceptibility.
Selection of construction material such as bricks, stone, steel, and concrete affect the selection of foundation. Settlement calculation of foundation is another factor relating to the loads from the structure and affects foundation choice.
A shallow foundation is preferred in the case of low-rise buildings. However, for high-rise buildings, a deep foundation is required. Deep foundations are provided because soils at greater depths are highly compacted.
Soil Bearing Capacity (SBC)
Soil bearing capacity is one of the foremost crucial criteria that affect the selection of the right foundation type. Decisions are often made to choose shallow or deep foundations according to the soil bearing pressure.
An allowable bearing pressure of a minimum of 100kN/m^2 or higher is effective for shallow foundations up to 4 stories. However, highrise structures can opt for a raft foundation given that the modulus of sub-grade reaction must not be exceeded while calculating.
Soil Types
There are different kinds of soil like sandy soil, loose soil, clayey soil, and expansive soil. A depth of 3m from the surface is termed topsoil. After 3m depth, the sub-soil begins. The bearing capacity of both the topsoil and subsoil layers influences the foundation selection to a great extent.
For a low-bearing-capacity soil, the stronger and suitable foundation should be selected compared to the soil with a strong bearing capacity. The bearing capacity is that the ability of soil to securely support structural loads without suffering shear failure and intolerable settlement.
Building Foundation is that structural part of the building that is below the plinth level. Being in direct contact with the soil transmits the load of the superstructure to the earth.
3.1 Clay Soil
Clay soil has a great capacity for water retention and that’s why great expansion and shrinkage occur in this kind of soil. The foundation structure may suffer from great settlement and uplift pressure in this type of. So, clay soil isn’t desirable. Applicable codes, such as The British standard, recommend a minimum depth of 1m for foundation and 3m if there are trees around.
Clay soil is best suited for Raft/Mat foundations to build upon. Ribs and beams are often incorporated into it to extend its stiffness. In case raft foundation is expensive, imposed loads are large, or a strong layer isn’t available at shallow depth, then under reamed pile can be selected.
The following is recommended in clay soil:-
A: Collecting and draining rainwater.
B: Foundation Extension to a depth where no moisture change occurs.
C: Removal of the shallow and weak soil layer, such as black cotton soil.
D: Construction in dry season if possible.
E: Uniform distribution of structural loads.
In the case where a shallow firm soil layer covers the soft clay soil layer, it’s always advisable to implement a wide reinforced strip Building Foundation . This way, the effect of loads on weak soil layer is reduced. Pile foundations are recommended for top-rise buildings and whenever uplift is predicted.
3.2 Peat Soil
It is considerably porous, easily compressible, and dark brown or black colour soil which is usually present near wetlands. It undergoes expansion and shrinkage thanks to moisture fluctuation and is extremely weak in terms of load-carrying capacity.
So, should be removed strong strata and strip Building Foundation is a good option for this soil. If the thickness of peat soil is great and its removal isn’t economical, then other Building Foundation types should be considered.
For example, concrete piles that are extended to the firm soil layer below, pad and beam foundation took to firm strata underneath for small projects, or foundation for the case where firm strata aren’t available at reasonable depth but there’s pave crust with 3-4m thick of suitable bearing capacity.
3.3 Silt
Silty soil, while being smooth to the touch, is mostly not suitable for Building Foundation structure due to its expansion. The expansion results in exerted pressure against the Building Foundation and may damage it.
The silty soil tends to retain moisture and doesn’t facilitate water drainage. Isolated pad footings and reinforced concrete spread are recommended if the silt or silty clay is stiff and extends to a great depth. The foundation depth should be greater than the erosion zone and also than the zone of swelling and shrinkage.
3.4 Sand and Gravel
Sand and gravel facilitate good water drainage and that’s why don’t cause structural movement. Moist compaction of soil and sand offer great support for foundation structure.
The bearing capacity is declined by half if gravel is submerged in water. Therefore, it’s important to stay the foundations as high as possible. A shallow, reinforced, wide strip foundation could also be suitable.
Sand tends to hold together reasonably well when damp, compacted, and uniform. But trenches may still collapse and thus, sheet pile is used often to retain the soil in the trenches until the concrete is poured.
If loose sand is extended for a greater depth, then it’s recommended to compact it and use spread footings. Alternatively, raft-driven pile, cast-in-place pile, or augured pile can be selected without the utilization of compaction energy.
Dry compact gravel, or gravel and sand subsoil are adequate for spread and strip foundations. Usually, a depth of 700mm is suitable for as long the ground has enough bearing capacity.
Ease of Construction
The selection of Building Foundation type should be made while keeping in mind the convenience with which it would be constructed at the site. Different types of foundations require labour with different skill sets and also different skill levels.
Water Table Level
The water table is another significant criterion that affects the foundation selection. The Building Foundation should not be placed on soil that undergoes expansion and contraction due to water table fluctuation. So, it should be constructed on entirely dry soil or wet soil.
A shallow footing or combined footing method is adopted when the formation level of the Building Foundation is below the groundwater table. Isolated footing is also a method used when this situation arrives.
It is a method used to avoid any overturning moments at the initial stages of construction caused by water, which occurs due to counteracting uplift pressure. In a situation where the above method cannot be executed, deep foundations like bored or micro piles are considered to provide the required uplift resistance.
Adjoining Structure/Water Bodies/Slopes
The selection of foundation types is done by using parameters like slopes, adjoining structures, and water bodies. The choice and safety decisions of the adjacent formation are influenced by whether or not the foundation of neighbouring structure is close to the target foundation.
The foundations of the adjacent structure are monitored to not be near the target foundation as it may affect the choice and hinder the process. The safety of the adjoining building is significant as it will affect the decision on the foundation type. It is more challenging if the neighbouring is an old property or a high-rise building.
Natural drain, vicinity to a slope, lake, closeness to a river are factors to consider. Buildings situated on sloping grounds use isolated RCC pad functions under stilts. The construction of residential buildings on slopes steeper than 25 degrees must strictly not be allowed.
7. Natural Disaster and Extreme Weather
A location that has experienced extreme weather or severe natural events is examined, and certain parameters and precautions will be considered. During the process of selecting the foundation, past data or records are examined. Whereby, creating a base for the selection process.
Economic Design
When there are several feasible foundation choices for the given project site, the economical factor may influence the selection of the foundation. Nonetheless, choosing an economical foundation should not compromise the safety, workmanship, strength, and durability of the foundation
Depth of foundation depends on the following factors:
- Adequate bearing capacity must be available.
- Factors that may cause considerable movements should be monitored such as depth of shrinkage and swelling in the case of clayey soils due to seasonal changes.
- Depth of frost penetration in case of fine sand and silt.
- The possible activity of excavation nearby.
- Depth of groundwater table
- The minimum practical depth of Building Foundation should not be less than 50 cm. To allow removal of topsoil and variations in ground level.
Hence the best-recommended depth of foundation is from 1.00 meters to 1.5 meters from the original ground level.
Base Preparation For Foundation
A concrete foundation should be constructed on firm undisturbed soil, engineered fill, or coarse gravel. Standing water, mud, frozen ground, and other debris should be removed. If the subgrade soil is of poor quality, it shall be excavated, and a layer of gravel 100mm thick shall be provided. The level tolerances for the prepared sub-grade shall not exceed +5mm, -15mm.
Standing water up to 25mm is to be displaced by the concrete if it fails to mix with water. It is required to develop a sound subgrade base for the footing to remove inappropriate materials below the designed bottom of the footing. In a case where there is over-excavation, it can be filled with engineered concrete.
Foundation Formwork
To achieve the required concrete surface finish, the formwork materials are selectively installed.
Joints between formwork panels are adequately sealed to prevent the leakage of grout during concrete casting and compaction.
Formwork is measured before concrete casting. It will confirm the top of concrete levels, location, and alignment.
In a situation where the formwork extends above the concrete level, the level is marked on the framework with a chalk line or with nails.
The Building Foundation framework is assorted and selected to meet the stiffness, stability to retain the weight of wet concrete during placement, and adequate strength.
To ensure no significant deformation of the framework during the process of concrete casting, the framework is stiffened as necessary.
Arrangement of Reinforcing Bars
To ensure the stability of the structure and continuity, reinforcement in the Building Foundation is crucial. It is highly important to monitor and study the areas which have been subject to earthquakes or if the area is on bad ground.
Steel reinforcement in the Building Foundation consists of strengthening bars placed transversely, longitudinally, or both, in the direction of the footing.
Longitudinal reinforcing is sometimes used to bridge minor trenches and soft spots or to increase strength over narrow excavations.
Transverse footing reinforcement is generally not needed unless the wall loads are high or soil-bearing capacity is poor.
The location of the longitudinal or transverse reinforcing bars will be at the center of the footing with a minimum cover of 75mm to the sides and bottom.
Foundation reinforcements can be set on bricks, chairs, construction, or other support devices.
The minimum distance of individual bars shall be 150mm.
The following items shall be visually approved and inspected after the installation of the rebar.
The minimum rebar size is 16mm.
The tolerance position of reinforcement bars shall not exceed ±6mm.
Reinforcement bars must be lapped to develop the bars’ full tensile capacity across the splice in case they cannot be installed in one length to meet the requirements.
Per ACI-318, a minimum lap length of 40 times the diameter of the reinforcement bar is required for splices in the reinforcement.
The separation between lapped or spliced bars is not to exceed 6 inches, or eight times the diameter of the reinforcement bar, whichever is less.
Concrete for Foundations
The strength of concrete should not be less than 17 MPa. This needs to be increased if the Building Foundation is exposed to aggressive environmental conditions and earthquake forces.
Concrete cover shall be 75mm for the Building Foundation in direct contact with soil.
Placement of concrete for footings can be by any conventional method, including direct chute, wheelbarrows, crane, pump, or conveyor.
Removal of Formwork
The time for stripping of formwork is 12 hours. The formwork is not removed earlier than 12 hours after completion of concrete finishing works.
Surface Defects Correction
After formwork is removed and curing completed, each concrete structure shall be visually inspected for surface defects. The points which shall be inspected shall be as follows:
Levels of finished concrete.
Alignment of Finished Concrete.
Levels and Alignment of embedded items such as anchor bolts.
Tolerances for levels and alignments
The finished surface of the concrete shall be checked for the following defects:
Honeycombs.
Spalling and dusting.
Cracks.
Depressions.
Bulges.
Abrupt irregularities
Repair of Foundation Surface Defects
Hack all cracked and unsound concrete up to a depth exceeding 50mm. Remove concrete behind rebar, in areas where rebar is exposed.
For corroded rebar, loose rust scales is removed by wire brushing. Treat the rebar with an anti-corrosion primer.
Feather edges are removed along the perimeter of the hacked area using a disc grinder.
Clean loose dust and dirt from the prepared surface using clean water. Use clean water to remove loose dust and dirt from the prepared surface.
Use hand-washed aggregates to pack clean into the hacked area to ensure they are secured with a fine wire mesh.
Use a secure framework with suitable ties to install a grout tight framework on a prepared surface.
Ensure prepared surface and aggregates achieve Saturated Surface Dry condition (SSD). Use a hand-operated grout pump through inlet ports to dispense clean water into the formwork assembly.
The gout is mixed in an adequate quantity of water by using a mixing drum. While stirring ensure that the grout achieves a homogenous consistency.
Use inlet ports to dispense grout mix into the formwork assembly. The process of grouting is started by the lowe-most inlet port. Lock-off the first port and grout through the adjacent inlet port as soon as the grout is observed appearing from the adjacent port. Follow the sequence of grouting until the entire formwork assembly is filled with grout.
Remove formwork assembly and cure using wet gunny sacks or curing compound.
Grind the surface to an even finish, if necessary.
Conclusion
Making the Building Foundation is a complex process and following the right processes and techniques is crucial. Shortcomings in the Building Foundation can result in serious structural defects like cracks, tilting, or even falling of the building. Getting the right construction partner is important. At Samruddhi we have just the right tools and manpower with the right skills and experience. Adhering to the right techniques and practices is a guarantee. Contact today for all your construction-related queries and needs.